Overview
The first photoresin for high-resolution 3D Microfabrication using Two-Photon Polymerization (2PP) is Nanoscribe GP-Silica. The ability to explore new applications in the microfluidics, microoptics, and other microtechnology fields is enabled by high optical transparency combined with thermal, mechanical, and chemical stability.
The main component of the Glass Printing Explorer Set, GP-Silica, was created as part of a collaboration with Glassomer.
Everything a user requires to print freeform microstructures made of fused silica glass is included in the Glass Printing Explorer Set. A successful print can be achieved with the help of the photoresin GP-Silica, silicon substrates, a number of print accessories, and comprehensive processing instructions that are included in the set.
These instructions include advice and tips for setting up print jobs, a pre-set of printing settings for the Solution Set Large Features, and thorough details on the thermal post-process.
Features
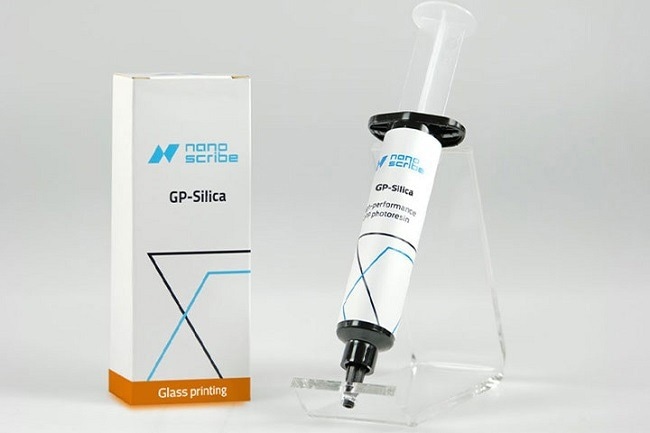
Image Credit: Nanoscribe
- The Glass Printing Explorer Set is intended for use in applications where thermostability, chemical, and mechanical stability, or optical transparency are polymer resins’ natural limits
- The development of novel applications in the life sciences, microoptics, and other fields that require the exceptional qualities of glass is encouraged by the two-photon polymerization (2PP) of fused silica glass
- The new photoresin GP-Silica is tailored for the large features in the 3D Microfabrication Solution Set
- High mechanical, chemical, and thermal stability
- Optical transparent from the UV- to IR-region
- Smooth optical quality surfaces
- Inorganic material for the exploration of new applications
GP-Silica has great potential for our research manufacturing complex microfluidics systems, although the required thermal post-processing is demanding.”
Nicolas Muller, College of Engineering and Architecture of Fribourg
Application
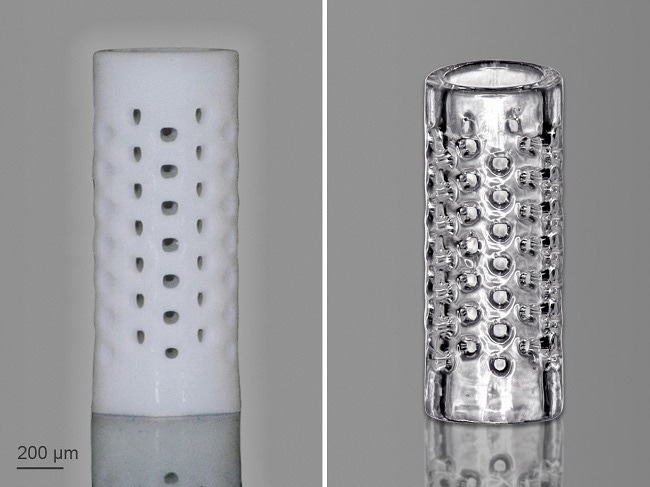
Green part of a 3D- printed filter tube (left) and corresponding filter tube after the sintering process (right). Glass is suitable for sterilization and typically biocompatible. Explore new applications in the field of life sciences with GP-Silica. Image Credit: Nanoscribe

Green part of a microfluidic nozzle (left) and the nozzle after the sintering process (right). Fused silica glass has a temperature resistance of more than 1000°C. Explore new, high temperature applications with GP-Silica. Image Credit: Nanoscribe
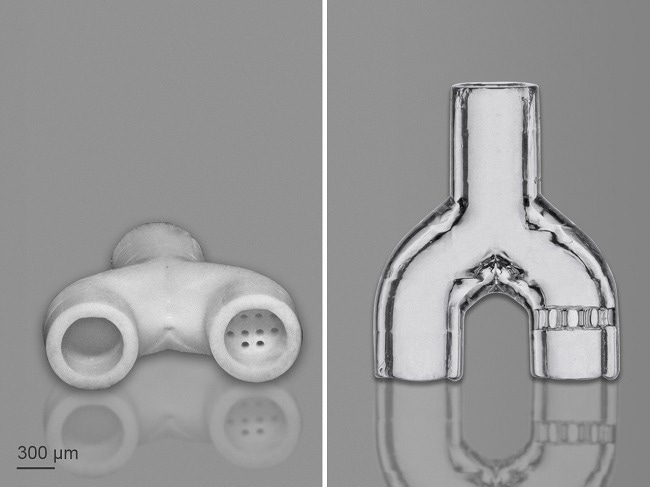
Green part of a microfluidics Y connector with integrated filter structures (left) and corresponding sintered glass structure (right). Image Credit: Nanoscribe
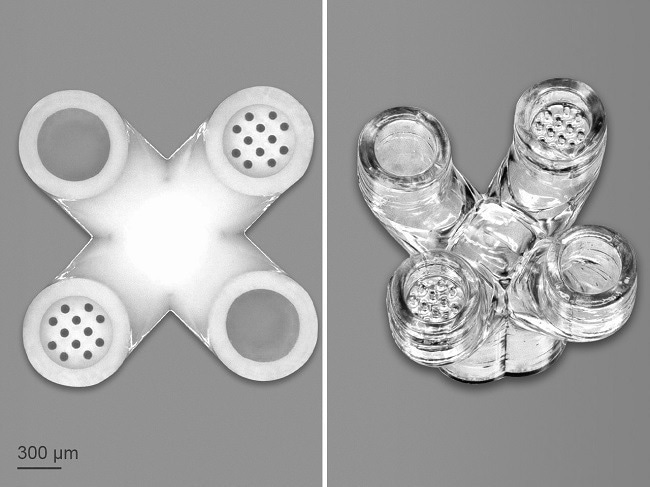
Green part of a complex microfluidic multi-connector (left) and corresponding sintered glass structure (right). Image Credit: Nanoscribe
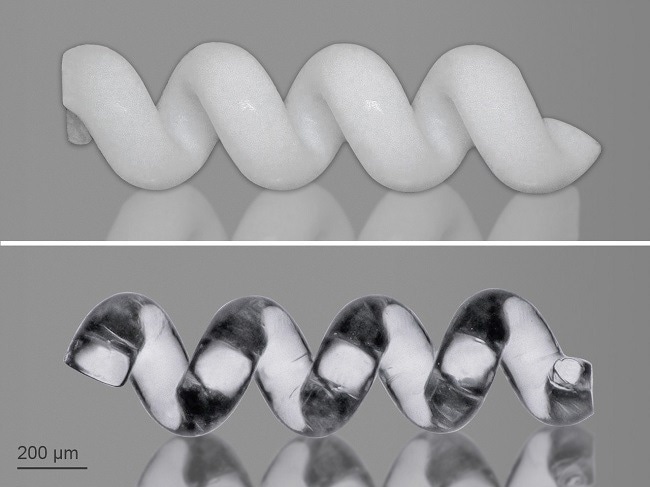
Green part of a microhelix (left) and the sintered helical microstructure (right). Glass features excellent mechanical characteristics. Explore new applications in the field of material engineering and MEMS with GP-Silica. Image Credit: Nanoscribe

Green part of a Tesla valve (left) and corresponding sintered glass structure (right). Glass features excellent chemical stability. Explore new applications in microfluidics with GP-Silica. Image Credit: Nanoscribe
Specifications
GP-Silica
Source: Nanoscribe
Properties |
GP-Silica |
IP-Q |
Young’s modulus [GPa] |
68.3 |
~ 5 |
Thermal stability [°C] |
> 1,000 a |
242 b |
Refractive index at 589 nm, 20 °C |
1.458 |
1.513 |
Lateral resolution [µm] c |
20 |
5 |
Post-processing |
Sintering |
- |
Surface roughness Ra [nm] c |
< 10 |
< 10 |
Sintering shrinkage [Vol. %] |
27 (isometric) |
- |
a Glass transition temperature Tg
b Degradation temperature
c Structure and print parameter dependent
Glass Printing Explorer set
- Everything a user requires to print freeform microstructures made of fused silica glass is included in the Glass Printing Explorer Set. A successful print can be achieved with the help of the photoresin GP-Silica, silicon substrates, a number of print accessories, and comprehensive processing instructions that are included in the set
- Advice and tips for setting up print jobs, a pre-set of printing settings for the Solution Set Large Features, and thorough details on the thermal post-process are provided
- The thermal post-process necessitates the use of an appropriate sinter oven. Using a customized sinter oven model made available by a business partner is recommended for the best results
Content of Glass Printing Explorer set
- GP-Silica
- Silicon substrates
- Print accessories
- Print and processing instructions
System requirements
- Nanoscribe Photonics Professional GT+/GT2
- Solution Set: Large Features
- Oven for thermal post-processing
Two-photon curable silica nanocomposite
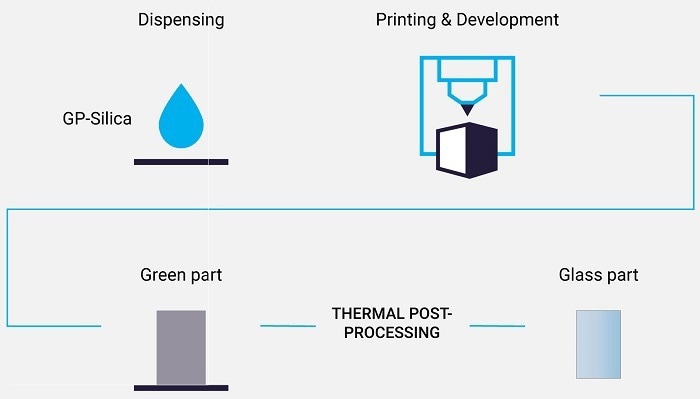
Process workflow: A CAD model is 3D-printed via 2PP-based microfabrication. The resulting green part consists of silica nanoparticles homogeneously suspended in a polymer binder matrix. In a two-stage thermal process, the polymer is first removed from the printed microstructure. In a second step, the silica nanoparticles fuse together to form the final microstructure of pure fused silica glass. Image Credit: Nanoscribe
- A renowned expert in shaping glass at room temperature, Glassomer GmbH, assisted in the development of the new printing material GP-Silica
- The new resin, which can be directly printed using Nanoscribe’s microfabrication systems, is a composite of silica nanoparticles dispersed in a photocurable binder matrix
- Two steps are necessary for the fabrication of GP-Silica:
- The GP-Silica is used to print the desired microstructures, and the so-called “green part” is produced by washing away the unpolymerized material
- The green component is thermally treated in the following step. The polymerized binder matrix is first removed at 600 °C before being subjected to a sintering procedure at 1,300 °C. The volume decreases as the silica nanoparticles join together in this step, exposing a 3D microstructure made entirely of fused silica glass
Glass. A new class of materials
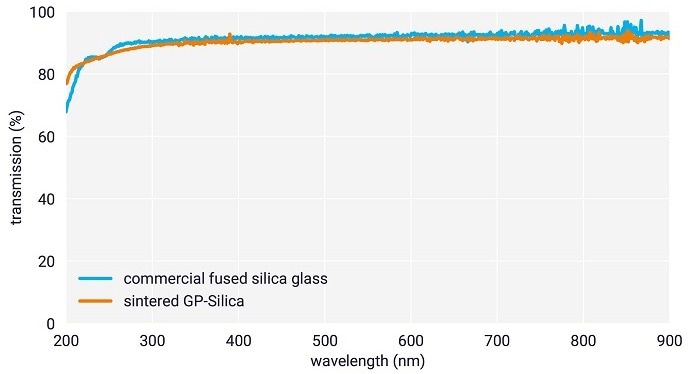
All organic compounds of GP-Silica are removed during post processing, resulting in 3D-printed structures of pure silica glass. The optical transparency of GP-Silica is identical to that of other commercially available fused silica. Image Credit: Nanoscribe
- A new material class created for 3D Microfabrication is introduced with GP-Silica. The high thermal and chemical stability of this brand-new inorganic print material is one of silica glass’s best qualities
- The new material is a strong candidate for imaging applications in the life sciences, microfluidics, microreactors, or microoptics, thanks to its optical transmission window, which stretches from 200 nm to the infrared region
- The new printing material offers new opportunities for MEMS and material engineering because its Young’s modulus is about ten times greater than that of traditional printing materials like IP-Q
- The IP Photoresins from Nanoscribe have been successfully used as printing materials for high-precision 3D microfabrication by Two-Photon Polymerization (2PP)
- The product line offers a wide selection of (meth)acrylate-based resins with negative tones that are intended for nano-, micro-, and mesoscale structures