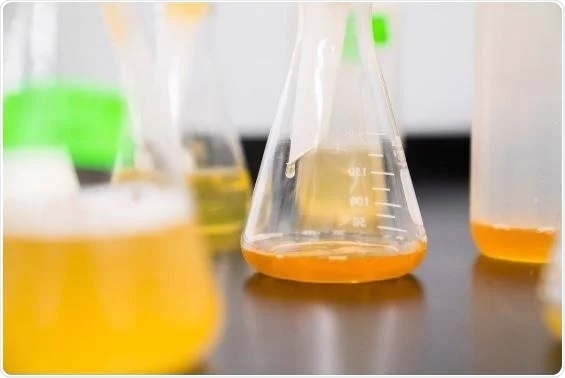
Image Credit: Thermo Fisher Scientific – Environmental and Process Monitoring Instruments
Pharmaceutical manufacturing is an industry that is both heavily regulated and exceptionally process-driven. A misstep in manufacturing can be expensive in the best-case scenario, and in the worst, it can endanger lives, especially if a product has already reached consumers.
The industry must comply with a number of guidelines set out by the Food & Drug Administration (FDA), for instance, the Current Good Manufacturing Practices (cGMP).
Product quality is at the core of cGMP, which ensures the appropriate monitoring, design and management of manufacturing processes and facilities.
cGMP also provides guidance for how to acquire good-quality raw materials, in addition to the management processes and systems preferred for maintaining the best laboratory testing procedures. All factors play a crucial role in the success and safety of pharmaceutical products.
For manufacturers, compliance with cGMP is a necessity, and while quality and safety are major concerns in the pharmaceutical industry, these guidelines do increase the number of challenges throughout the manufacturing process.
Accelerating processes and outputs without compromise
Even the minimal amount of contaminant can drastically impact results, and the broad range of active pharmaceutical ingredients (APIs) used means that verifying raw materials is a key step in the production process.
For the verification of materials, samples are typically sent to labs outside the manufacturing floor for analysis to a team of highly trained professionals. While this verification process is very accurate, it is liable to bottlenecks and leads to frequent stoppages in production.
Challenges arise when regulations demand the sampling of a statistical number of containers for a delivered material (sqrt n+1), but now the industry is moving in the direction of the verification of every single container of a delivered material (100 percent material verification).
While a trusted method, it is key to consider the size of delivery when using 100 percent material verification to strengthen production safety; this requirement means facilities could be required to verify one drum or 1,000 drums per day.
The collection of batches to test will increasingly become labor-intensive and time-consuming, which will intensify the bottleneck issue. Another obstacle later on in the production line.
Solvent drying, which is the partial or complete removal of a solvent or solvents from an intermediate or API, occurs in a wide range of process vessels, including vacuum dryers, tray dryers and rotary dryers.
Previously, testing the success of solvent drying could only be carried out when the process had finished, which again required outsourcing the testing of samples to a separate or external lab.
If a test failed, the product had to re-enter the drying process, resulting in slow production times and the potentiality of over-drying the solvent, resulting in a lost batch.
It is no longer feasible to assign the testing of drying samples and raw materials to separate or external laboratories due to the sheer number of test batches. Pharmaceutical manufacturers are searching for new tools that have the capacity to accelerate the process of verification without compromising the accuracy of results.
Technologies rising to the challenge
Presently, technological progress is being made in bringing the power and accuracy of the lab to the manufacturing floor. For example, new spectroscopy technology is eliminating the need for wet chemistry testing, facilitating raw material ID and other analyses to take place on the warehouse floor rather than a lab.
Those in charge of accepting shipments and handling the inventory of raw materials can quickly test a sample by using a portable, user-friendly device for the verification of materials such as ionic salts, including potassium chloride and sodium chloride, which are extensively used in injectables, buffers and biologics.
As well as accelerating raw material verification, analysis of the material in its original packaging means these tools also reduce the risk of cross-contamination and get rid of the need to transport the materials through numerous locations.
Process mass spectrometers have the capacity to precisely measure individual solvent concentrations in multiple dryer vents and to monitor the drying process at a different part of the production line.
Manufacturers now have the capacity to make rapid amendments to heating and temperature durations by having an advanced understanding of the emissions from APIs on the drying tray.
When used appropriately, process mass spectrometers limit the risk of product loss due to over-drying, and they can also accelerate the production process while reducing the dependence on time-consuming offline testing such as Loss on Drying (LOD).
This online technique improves batch-to-batch quality, significantly reduces interruptions to the process, and shortens drying times.
Accelerating innovation through simplification
As with many other industries, technological progress makes the pharmaceutical industry a much safer and more productive workplace.
Manufacturers can speed up production times and improve innovation with uncomplicated testing and analysis by reducing the dependency on lab testing and assigning their highly technical staff towards R&D.
Additionally, the time of factory floor workers can be better spent while maintaining compliance with cGMP and other regulations.
Acknowledgments
Produced from materials originally authored by O. Dean Stuart and Daniel Merriman from Thermo Fisher Scientific.
About Thermo Fisher Scientific – Environmental and Process Monitoring Instruments
We design and manufacture industry-leading products for Gas & particulate pollutants, Flow, gas and liquid measurement, Process analytical measurements, and Industrial Hygiene.
Technologies have proven to help customers improve efficiency, ensure process and quality control, maintain regulatory compliance, and increase worker safety.
Process mass spectrometers
Maximize product yield and increase profitability with process mass spectrometry analysis. Process gas analyzers are engineered to meet a number of challenging process applications in the petrochemical, iron, and steel, and biotechnology industries. Highly reliable and easy-to-own, Thermo Fisher Scientific process gas analysis technologies deliver faster, more complete, lab-quality online gas analysis and process analytics. Learn More
Process Analytical Technology/Biopharma
Process Analytical Technology (PAT) is a regulatory framework initiated by the United States’ Food and Drug Administration (FDA) that encourages pharmaceutical manufacturers to improve the process of pharmaceutical development, manufacturing, and quality control.
PAT aims to improve process efficiency by defining Critical Process Parameters (CPP) and monitoring these CPPs to stay within a defined limit, either in-line or on-line to maintain a product’s Critical Quality Attributes (CQA). Monitoring CPPs with process mass spectrometry gas analysis reduces over-processing, pinpoints contaminants, and increase product consistency. Learn More
Industrial hygiene
Industrial hygiene instruments keep your investments secure, your facilities compliant with local regulations, and your workers safe from leaking pollutants, gases, or toxic vapors. Make sure you have the most updated technology, with access to repair and calibration support to maintain reliable gas monitoring. With our environmental expertise, you can breathe easy knowing your company, workers, and neighboring communities have cleaner, safer, and healthier air quality. Learn More
Sulfur analyzers
Online sulfur analyzers replace expensive and time-consuming laboratory sampling. Get fast responses and wide measurement ranges of trace sulfur and total sulfur in flare gas, liquid, and vapor for reliable emissions monitoring. Learn More
Gas & particulate analyzers
Increasingly stringent regulatory requirements are making it more difficult to maintain regulatory compliance and optimal process performance. Air quality monitoring and reporting requirements in the U.S., China, India, Europe, and Latin America are shifting and being redefined. Together we can arrive at solutions that make sound business sense. Learn More
Flow measurement
Flow measurement and process control are critical aspects of producing, handling, and transporting hydrocarbons around the world. With our Thermo Scientific suite of flow computers and flow meters, we enable our customers to reduce cost, decrease lost material, automate, and monitor critical points in processes. From field to control room and upstream to downstream, our products provide greater control, confidence, and reliability. Learn More
Sponsored Content Policy: AZO Life Science publishes articles and related content that may be derived from sources where we have existing commercial relationships, provided such content adds value to the core editorial ethos of AZO Life Science, which is to educate and inform site visitors interested in medical research, science, medical devices, and treatments.