Produced in Partnership with RETSCH GmbHReviewed by Emily MageeApr 4 2023
A solid sample material always has to be sufficiently prepared by homogenization and size reduction before it is exposed to physical or chemical analysis. Operators should also take care to ensure that the analysis sample completely represents the original material and that the sample preparation process is reproducible. Only then can meaningful results be guaranteed.
Most sample materials can be minimized to the desired analytical fineness at room temperature if a mill with a suitable size reduction principle (cutting, shearing, friction, impact, pressure) is chosen.
However, size reduction at room temperature has limitations. For example, a minor increase in temperature may negatively affect the sample, or if the material is very elastic, the size reduction principles discussed above may cause deformation.
Cold or cryogenic grinding is the ideal solution for such samples. This entails the use of grinding aids, such as liquid nitrogen (-196 °C) or dry ice (-78 °C), that embrittle the sample by cooling and enabling breakage to occur more easily. This also allows the volatile components of the sample to be preserved.
This article discusses which sample materials are suitable for cryogenic grinding, which laboratory mills are appropriate, and which other factors must be considered.
What Materials are Suitable for Cryogenic Grinding?
Samples with Elastic Behavior
Numerous polymers (plastics such as PA, PP, PET, etc.) and other materials exhibit visco-elastic behavior during grinding, which causes plastic deformation. This indicates that a crack initiation, i.e., a breakage, does not occur.
Elastomers such as silicone baking dishes and rubber tires, which are utilized at room temperature because of their flexibility, have a “glass transition temperature” much lower than room temperature.
The elastic plastic sample’s temperature falls below the glass transition temperature if they are immersed in liquid nitrogen; this lowers the material’s ability to resist high mechanical stress by either viscous flow or elastic-plastic behavior. If this pre-cooled material is then ground in a mill, the sample is expected to show brittle breaking.
Cryogenic grinding can also be applied hard plastics, despite them already being brittle at room temperature. The sample temperature should not surpass the glass transition temperature to attain an effective size reduction process.
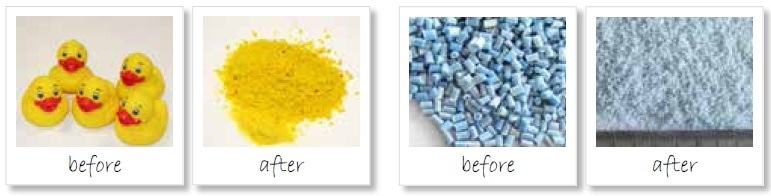
Image Credit: RETSCH GmbH
Samples with Volatile Components
Materials that have volatile components such as solvents (PCB, PCP, toluene, benzene, etc.) are difficult to properly prepare for analysis as a temperature increase during grinding may cause a loss of the analytes. The grinding process increases the particle surface, further enhancing the emission of volatiles.
The low temperature of liquid nitrogen or dry ice considerably reduces the high vapor pressure of the components, embrittling the sample matrix. As a result, the volatile components are not significantly impacted by the relative temperature increase which takes place during the grinding process.
Biological and Medical Samples
Biological samples prepared for extraction of nucleic acids from animal/human tissue, plants, yeast, or bacteria can sometimes be highly temperature-sensitive during and after the process and may even be destroyed.
In these conditions, cryogenic grinding supports the process by embrittling groups of cells and cell walls, enabling them to disrupt more easily and decreasing the speed of the subsequent decomposition of the cell fragments.
Undesired cell reactions are virtually “frozen” by immersing the sample into LN2, allowing cell activities to be observed later.
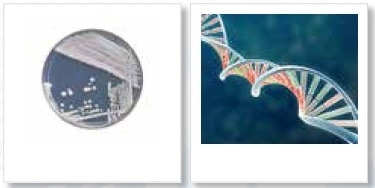
Image Credit: RETSCH GmbH
Sticky or Tough Food Samples
Sticky or tough sample materials such as marzipan, raisins, wine gum, or cheese clump together when they are ground at room temperature and are not sufficiently homogenized. The low temperature of the cryogenic process prevents the sample from clumping so that it is fully homogenized and suitable for analysis.
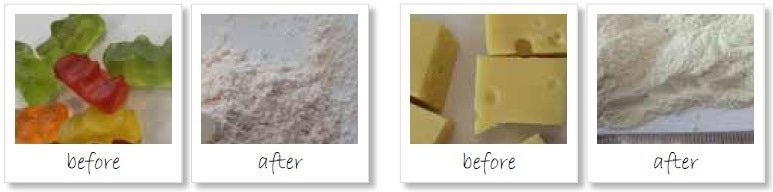
Image Credit: RETSCH GmbH
Overview Applications
Table 1. Source: RETSCH GmbH
Sample |
Mill |
Accessories |
Feed quantity |
Grinding time |
Speed |
Final fineness (d90) |
Gummy bears |
MM 400 |
- 2 grinding jars stainless steel 50 ml
- 2 grinding balls 25 mm stainless steel
- CryoKit, liquid nitrogen
|
10 pieces |
1 minutes |
30 Hz |
< 300 µm |
Caoutchouc |
CryoMill |
- grinding jar stainless steel 50 ml
- grinding ball 25 mm stainless steel
- liquid nitrogen
|
4 g |
2 minutes |
30 Hz |
< 500 µm |
E. coli bacteria |
CryoMill |
- grinding jar stainless steel 50 ml
- grinding ball 25 mm stainless steel
- liquid nitrogen
|
10 ml frozen cell pellets |
2 minutes |
30 Hz |
complete cell disruption |
Plastic granulate |
ZM 200 |
- 12-tooth push fit rotor
- distance sieve 0.5 mm
- cyclone
- liquid nitrogen
|
40 g |
20 seconds |
18,000 min-1 |
< 500 µm |
Refuse-derived fuels |
ZM 200 |
- 12-tooth push fit rotor
- distance sieve 0.75 mm
- cyclone
- 300 g dry ice
|
150 g |
30 seconds |
18,000 min-1 |
< 0.75 mm |
Wine gum |
GM 300 |
- grinding container stainless steel
- full metal knife
- cryo lid with aperture
- dry ice
|
500 g |
40 seconds and 20 seconds |
1000 min-1 and 4000 min-1 |
< 0.8 mm |
Rubber duck |
SM 300 |
- parallel section rotor
- 2 mm bottom sieve
- liquid nitrogen
|
5 pieces |
40 seconds |
3000 min-1 |
< 2 mm |
Pills with liquid filling |
RM 200 |
- mortar and pestle stainless steel
- liquid nitrogen
|
40 pieces |
3 minutes |
100 min-1 |
< 250 µm |
Suitable Lab Mills for Cryogenic Grinding
Several aspects must be considered when selecting an appropriate laboratory mill for cryogenic grinding. Although the sample volume is crucial for the decision, the preferred final fineness and the feed size are also important factors. The mixer mills MM 400 and CryoMill are specifically designed for processing small sample volumes.
These mills often attain finer grind sizes, even with intricate plastic samples, than, for example, rotor mills, as the sample is left behind inside the closed grinding jar for a longer period when compared to the open grinding chamber of the rotor mills.
The sample is cooled continuously for the whole grinding process in the CryoMill, even with a constant temperature of -196 °C.
Mortar grinders, cutting mills, knife mills, or rotor mills process substantially larger feed sizes and sample volumes than mixer mills. However, the size reduction principles of these mills typically produce larger grind sizes, especially with grinding plastics.
The Knife Mill GRINDOMIX GM 300 is most appropriate for the cryogenic grinding of food samples, with the restriction that only dry ice may be used since the mill is not designed for temperatures as low as -196 °C. However, both liquid nitrogen and dry ice may be utilized for cutting and rotor mills as grinding aids.
Liquid nitrogen is particularly suitable for materials with a glass transition temperature lower than -50 °C due to its extremely low temperature. The benefits of dry ice include that it does not evaporate as quickly as liquid nitrogen and may be mixed with the sample for grinding, lengthening the cooling effect.
This is particularly beneficial for materials with a low thermal capacity, i.e., those incapable of holding a low temperature, such as thin plastic foils. Sample feeding with dry ice is usually simpler, especially if the particles are less than 1 mm, as opposed to extraction of the material from liquid nitrogen.
Furthermore, it is safer to handle dry ice because the danger of asphyxiation, for instance, is minor. In addition, dry ice does not splash during grinding as it is mixed thoroughly with the sample material.
Irrespective of these aspects, suitable safety regulations should always be observed when handling cryogenic grinding aids.
The following section will outline a range of laboratory mills ideal for cryogenic grinding.
Mixer Mills MM 400 and CryoMill
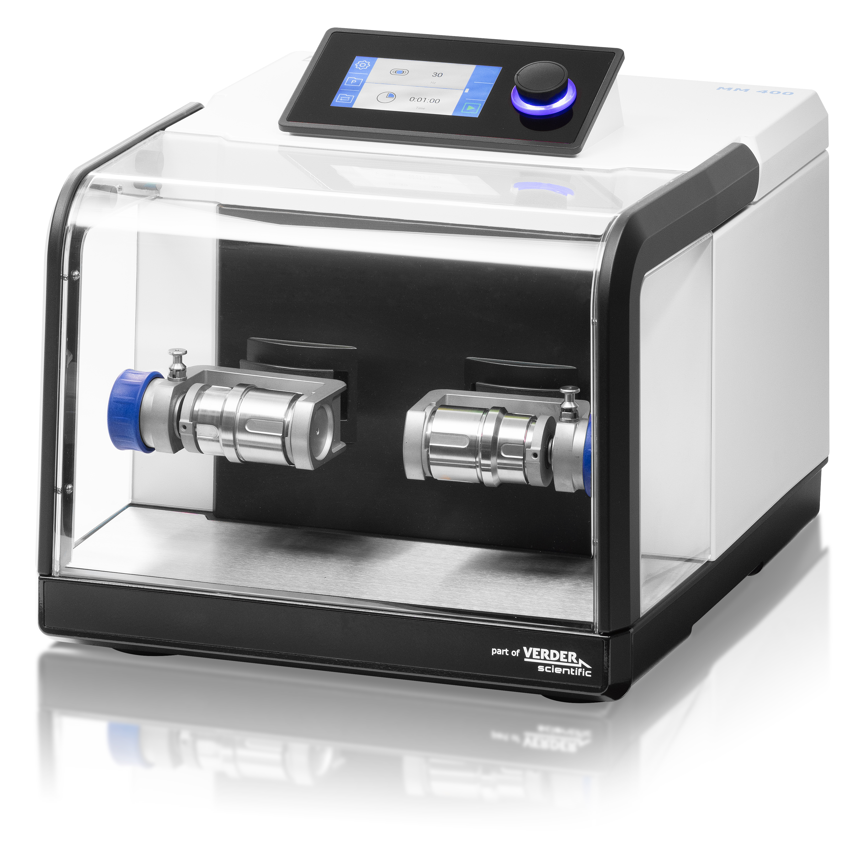
Mixer Mill MM 400. Image Credit: RETSCH GmbH
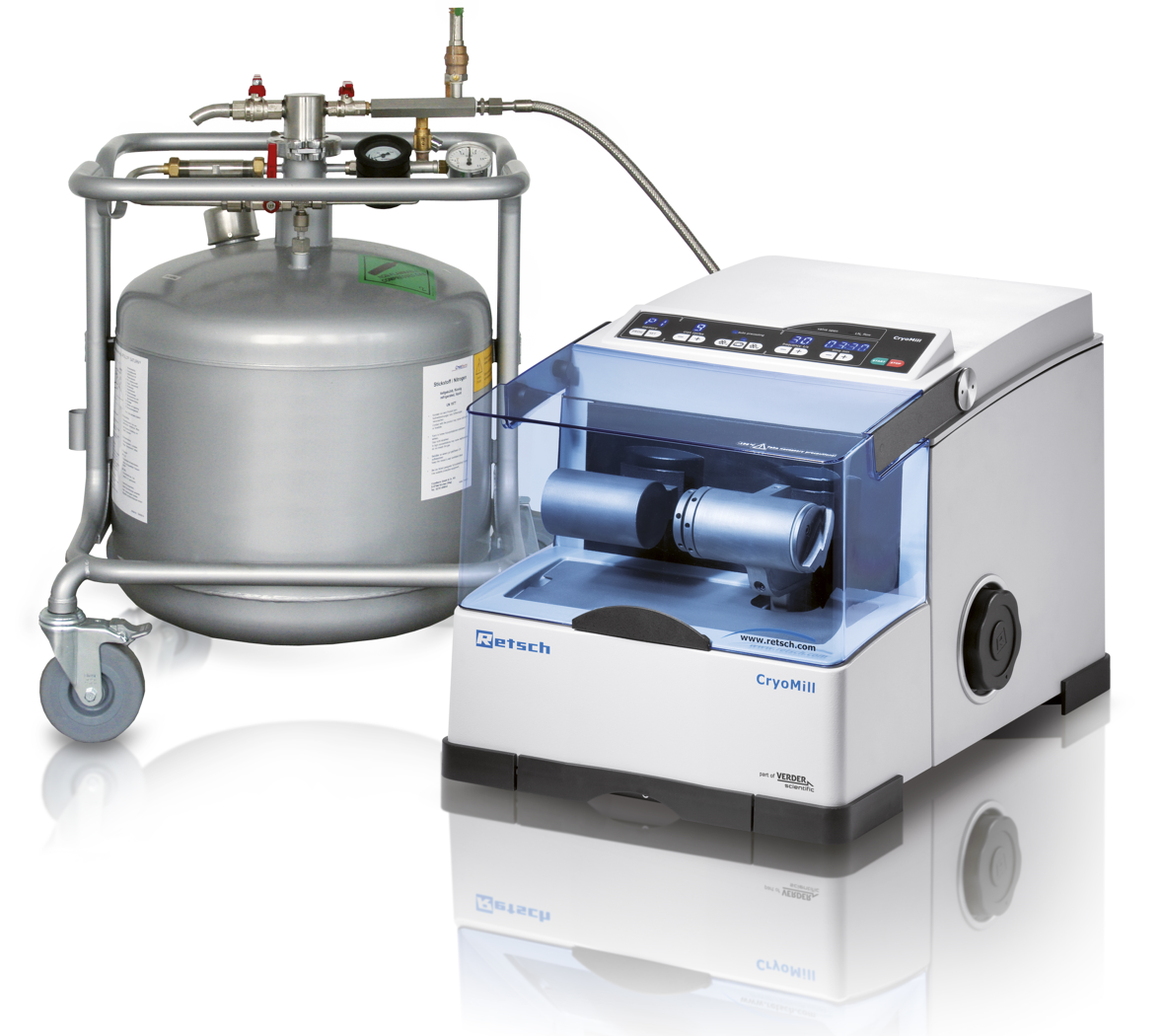
CryoMill with 50-liter tank. Image Credit: RETSCH GmbH
The mixer mills MM 400 and CryoMill are ideal for homogenizing small sample volumes with the greatest feed size of 8 mm. These mills have one or two grinding stations, respectively, into which the screw-top grinding jars are safely clamped for grinding.
These screw-top grinding jars are filled with grinding balls and the sample. The closed grinding jars, and therefore the sample, are embrittled with the use of liquid nitrogen.
Suitable grinding jars of the MM 400 are made of steel of PTFE; single-use vials of 1.5, 2 and 5 ml are also offered. It is worth noting that liquid nitrogen should not be enclosed in the grinding jars.
LN2 enters the gaseous phase as a result of the frictional heat of the grinding process, causing a substantial increase in pressure within the grinding jar. Using tongs, the closed grinding jar is placed in an insulation container filled with liquid nitrogen for two to three minutes and then clamped into the MM 400.
Due to the high energy input and the consequent frictional heat, the grinding process should not exceed 3 minutes to prevent the sample from warming up and therefore maintaining its breaking properties. These should be disrupted by intermediate cooling of the closed grinding jars in case longer grinding times are required.
The CryoMill, however, has the advantage of providing continuous cooling of the grinding jar with liquid nitrogen, lowering the temperature of the jar and sample to -196 °C in just a few minutes. This means a consistent temperature of -196 °C is ensured even for long grinding times, without the need for intermediate cooling cycles.
Additionally, at no point does the user come into contact with liquid nitrogen, making the operation of the CryoMill safe and user-friendly. The automatic pre-cooling function ensures that the grinding process only begins after a temperature of -196 °C is met and maintained. A zirconium oxide grinding jar is available for heavy-metal-free grinding.
Ultra Centrifugal Mill ZM 300
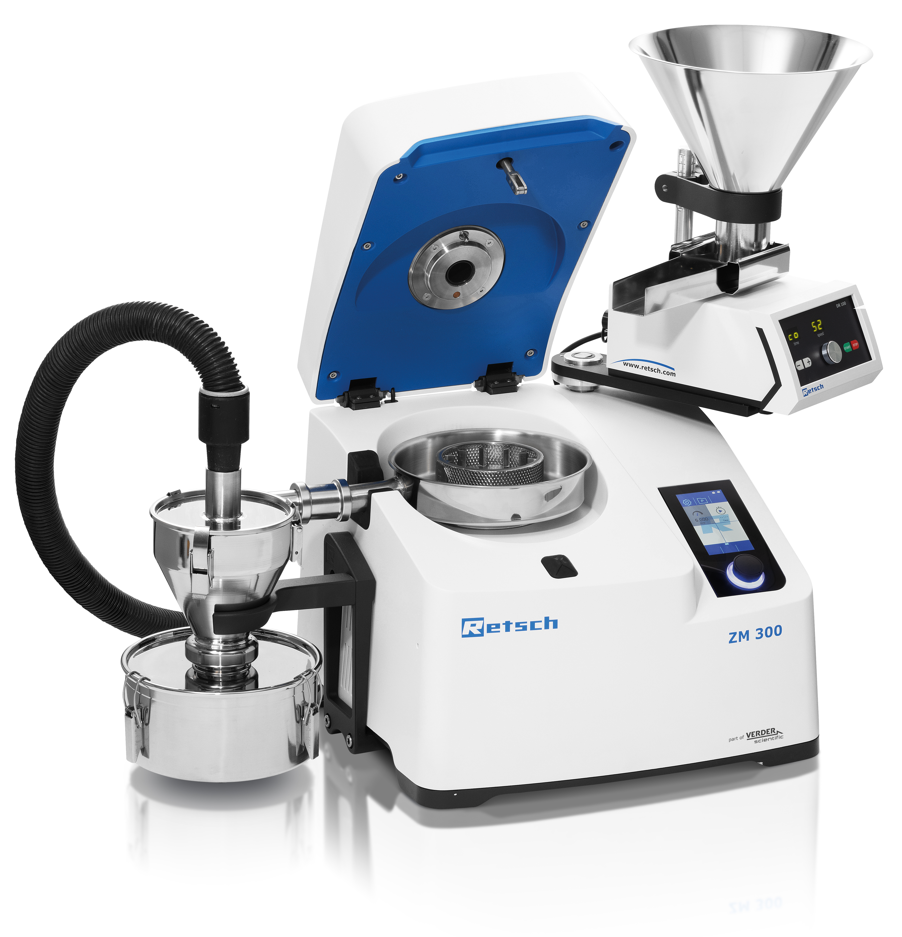
Ultra Centrifugal Mill ZM 300 with cyclone. Image Credit: RETSCH GmbH
The Ultra Centrifugal Mill ZM 300 is an alternative mill that is entirely appropriate for cryogenic grinding as it allows larger sample volumes than the mixer mills. This high-speed rotor mill is even capable of pulverizing some types of elastomers, such as polystyrene, without cooling.
However, embrittlement of the material is necessary in most cases. The sample, which can be granulate or pre-cut molded parts, is directly immersed in a container filled with LN2 and is continuously yet slowly fed into the hopper of the ZM 300 with the use of a steel spoon.
If the sample has a high fat content or is extremely heat-sensitive, embrittlement usually improves the grinding process as the effects of the frictional heat are counteracted by the cooling.
When dry ice is used as a grinding aid, it must be mixed with the sample in a 2:1 ratio and then the ZM 300 pulverizes the complete mixture. Dry ice is pure carbon dioxide and thus evaporates from the sample without residues.
It is recommended to use a cassette along with a cyclone to ensure that CO2 and residues of LN2 evaporate during the grinding process.
Cutting Mill SM 300
The previously discussed factors that affect the choice of a grinding aid are also relevant when conducting cryogenic grinding in the Cutting Mill SM 300. This mill is particularly suitable for processing tough materials, such as shoe soles or bitumen, and offers feed sizes larger than the ZM 300.
The SM 300 can homogenize even embrittled and roughly cut car tires. The embrittled sample material is rather hard; thus, it is recommended to use the 6-disc rotor as it works more like a shredder. It can also be utilized to cut heterogeneous samples such as frozen chicken parts, including bones.
Due to the constant cooling effect throughout the grinding process, it is advised for dry ice to be utilized for grinding thin plastic foil, which is normally a part of refuse-derived fuels.
Knife Mill GRINDOMIX GM 300
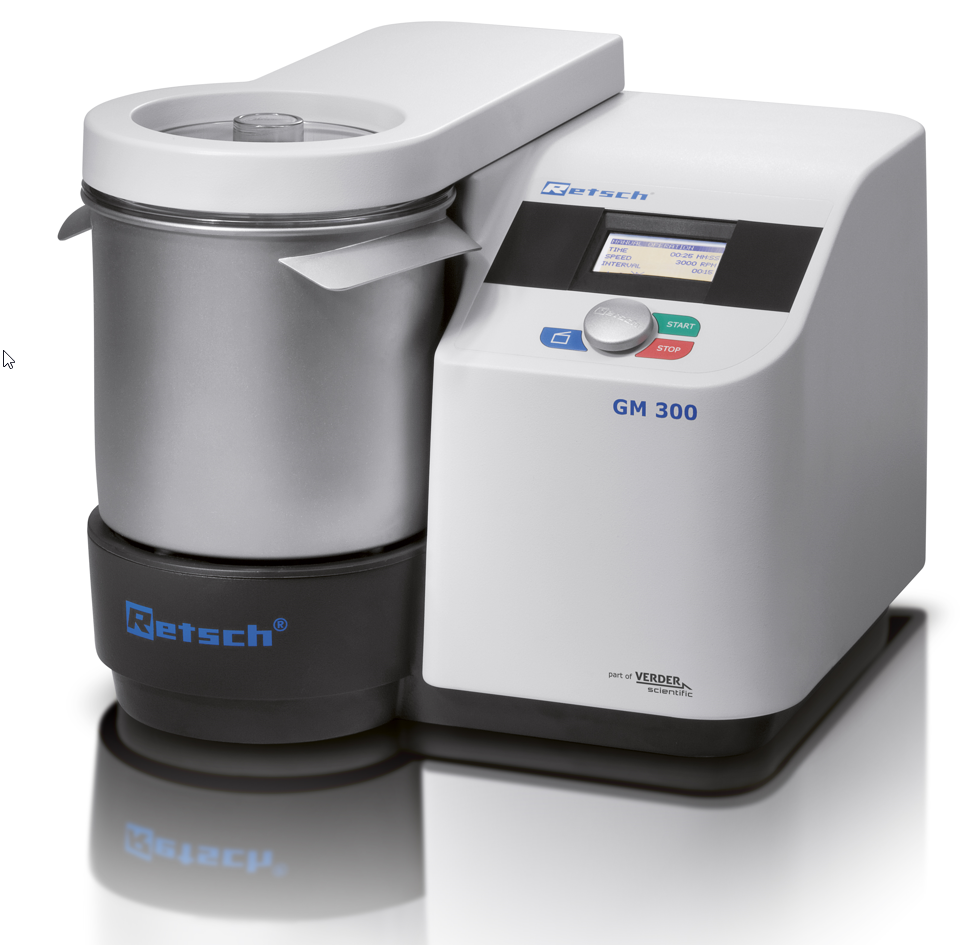
Knife Mill GRINDOMIX GM 300 with steel container.
Image Credit: RETSCH GmbH
Tough and sticky food samples such as marzipan, raisins, cheese, or wine gum may be perfectly homogenized with the Knife Mill GRINDOMIX GM 300. Even chocolate, which can easily become paste-like when processed at room temperature, can be successfully cryogenically pulverized.
The sample is subsequently combined with dry ice in a 1:2 ratio. After several minutes, it is fully cooled, and the grinding process begins. The dry ice maintains the cooling of the sample throughout.
No plastic accessories should be utilized when performing cryogenic grinding in the GM 300, as these may be damaged during the process. Instead, a full metal knife, a grinding container made of stainless steel, and a lid with an aperture to enable evaporation of the gaseous carbon dioxide are suitable accessories.
Mortar Grinder RM 200
Friction and pressure are utilized to pulverize samples in a mortar grinder, with these samples undergoing the grinding process for as long as required to achieve the desired final fineness.
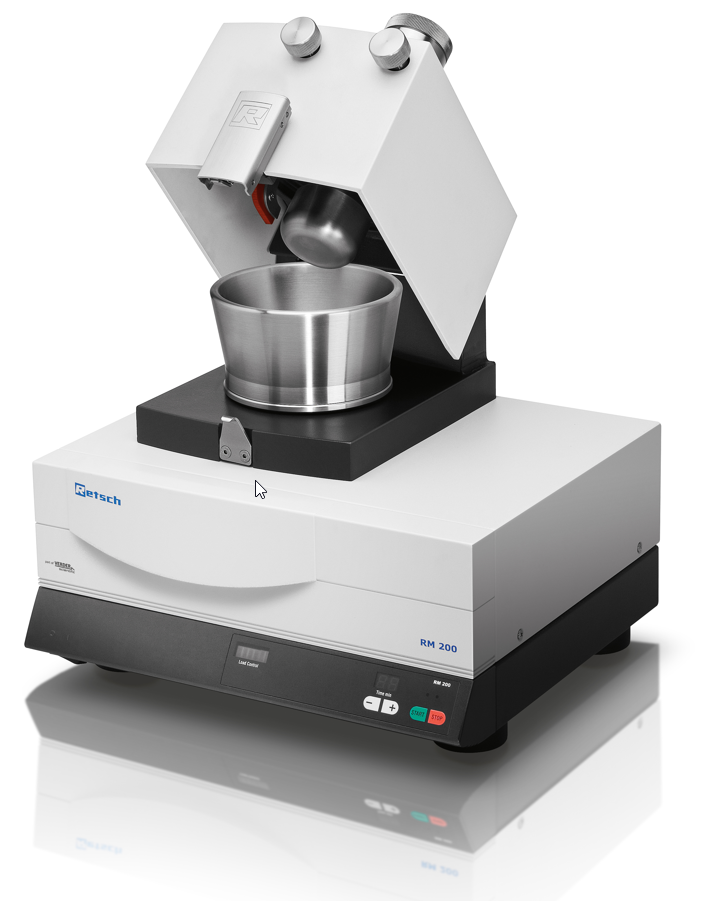
Mortar Grinder RM 200 with steel mortar.
Image Credit: RETSCH GmbH
The Mortar Grinder RM 200 is not a closed system. This means liquid nitrogen or dry ice may be added during grinding using a window in the cover. A pestle and mortar made of stainless steel are required for cryogenic applications. For example, a mortar grinder can effectively pulverize tablets with liquid filling.
Overview RETSCH Mills for Cryogenic Grinding
Table 2. Source: RETSCH GmbH
Mill |
Feed size 1,2 |
Max. feed quantity 1,2 |
Final fineness 1,2 |
Remark |
CryoMill |
< 8 mm |
1 x 20 ml |
50 µm |
- Continuous grinding under cryogenic conditions
- User comes at no point into contact with LN2
- Zirconium oxide grinding jar available for cryogenic applications
|
MM 400 |
< 8 mm |
2 x 20 ml |
100 µm |
- Sample is placed in leak-free grinding jar of steel or PTFE and embrittled before grinding
- Intermediate cooling may be necessary
|
ZM 200 |
< 10 mm |
4000 ml |
300 µm |
- Embrittlement with LN2, e. g. of samples with glass transition temperature < -80 °C
- Dry ice is best suited for materials with low thermal capacity
- Dry ice is preferably used for samples with a particle size < 1 mm
- Use of cyclone is mandatory
|
GM 300 |
< 40 mm |
2000 ml |
500 µm |
- Dry ice is best suited for materials with low thermal capacity
- Dry ice cools the sample during grinding
- Full metal knife used together with stainless steel grinding container and a special cryo lid
|
SM 300 |
< 80 mm |
4000 ml |
2000 µm |
- Cryogenic grinding only with 6-disc rotor and cyclone
- Bottom sieves 2 – 20 mm suitable for cryogenic applications
|
RM 200 |
< 8 mm |
< 190 ml |
10 µm |
- Dry ice or LN2 can be added during grinding
- Only use mortar and pestle made of stainless steel
|
1 Depending on sample material and grinding parameters
2 Volume may differ for applications without cryogenic grinding aids
Conclusion
For many materials, pulverization with liquid nitrogen or dry ice is the only way of acquiring a sample that is suitable for subsequent analysis. RETSCH offers a variety of laboratory mills that enable gentle and efficient cryogenic sample preparation.
The utilization of these mills significantly reduces both the cost and labor required for low-temperature grinding. A range of suitable accessories guarantees that the grinding process is performed safely.
Acknowledgments
Produced from materials originally provided by RETSCH GmbH..
About RETSCH GmbH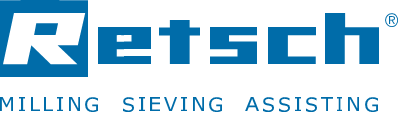
With more than 100 years of experience in sample preparation, RETSCH is the world’s leading manufacturer of instruments for homogenizing laboratory samples for analysis as well as for analyzing the particle size of solid substances by test sieving.
The RETSCH product portfolio includes a great variety of mills and jaw crushers, capable of reducing materials down to any required fineness, sieve shakers and test sieves as well as assisting technologies to optimize the handling of samples.
RETSCH instruments stand for representative sample preparation in compliance with relevant standards and contamination-free comminution processes – they are essential tools for preparing samples for laboratory analysis and stand for reliability, precision and durability.
Since 1990 RETSCH is part of the continuously growing technology group VERDER and forms the core of the group’s Laboratory Division VERDER SCIENTIFIC. Other companies belonging to this division are Retsch Technology GmbH, ATM GmbH, Eltra GmbH and Carbolite Gero Ltd.