Roughly 10,000 years ago, humans were witness to one of mankind’s greatest discoveries. To help preserve their food, humans were storing products, such as milk and fruit juices, in jars and skins. However, when they opened the vessels in which they had been keeping these precious goods, they found that their composition had changed.
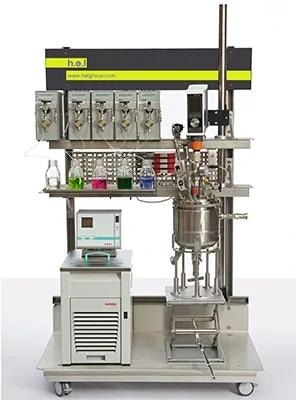
Image Credit: H.E.L Group
The activity of microorganisms transformed the stored products in a biological process called fermentation.
Unlike the majority of macroscopic creatures that use oxygen to oxidize the nutrients they ingest to obtain energy, fermentative organisms use alternative routes to oxidize sugars to get the cellular power they need to live. For example, Saccharomyces cerevisiae transforms glucose in the malt into ethanol, transforming it into beer, and Lactobacillus converts lactose into lactic acid, resulting in cheese.
Perhaps unsurprisingly, humans noticed this change and observed that the end product’s organoleptic properties had improved compared to the original.
Much like they had already done with animals and plants, people decided to domesticate microorganisms for their benefit. Unlike the cultivation of animals and plants, for which we had to build pens and dig burrows, the requirements of microorganism cultivation are somewhat different.
Several conditions are needed for fermentative microorganisms to thrive, including high humidity and a lack of oxygen (anaerobiosis). The need to replicate these conditions unleashed humanity’s creative side, forcing the design of vessels and containers that would maintain these conditions. These early receptacles were the origin of bioreactors or fermenters.
The first evidence of the original bioreactor - a pottery vessel used explicitly for fermentation – has been dated back to 7,000 BCE in China. This early form of fermentation was used to ferment a mix of honey, rice, and fruit.

Image Credit: H.E.L Group
The second oldest evidence of fermentation occurred 1,500 years later and was found in Iran. This paved the way for the development of other fermented products, including pickled cucumber in the Tigris Valley around 2000 BCE and leavened bread in Egypt around 3000 BCE.
Although commonly used for culinary purposes, as is well-known today, fermentations can also have medicinal properties. This discovery was perhaps first made by Chinese fermenters in approximately 500 BCE when they discovered that infected wounds could be effectively treated with moldy fermented soybeans.
Though they observed the effective healing properties, they likely did not know that they were using penicillin, which is produced by a fungus.
In fact, humanity needed to wait over 2,400 years until penicillin itself was discovered in a serendipitous event. Dr. Ian Fleming returned from his holiday and found that some mold was contaminating his Staphylococcus cultures growing on Petri dishes.
It was that mold, subsequently named Penicillium rubens, which Fleming noted inhibited the growth of bacteria. It did this by producing chemicals that prevented the other microbes from proliferating.
Though this discovery is today known to be vital, it was initially dismissed. Only when Fleming et al. demonstrated an increase in the survival of mice infected with Staphylococcus, the discovery began to reap the attention it rightly deserved.
At that time, however, the process of producing penicillin was labor-intensive, painfully slow, and resource-consuming, and the production of the broth which was used to grow the fungus took place in whatever containers could be found, including bathtubs and bedpans.
Researchers had been advancing in the development of reactors that would be used for microbial growth up until just before the discovery of penicillin.
In Manchester, in the United Kingdom, a researcher named Chaim Weizmann developed large vessels which were able to maintain conditions suitable for the microorganism production of acetone, which was in turn used for manufacturing explosives.
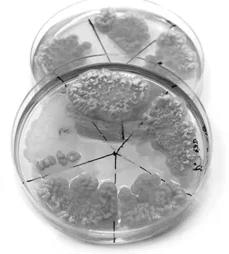
Image Credit: H.E.L Group
Other discoveries were made by Strauch and Schmidt, who developed tubing for the introduction of water and steam to clean the reactors and achieve aseptic conditions.
A push for the development of bioreactors resulted from the need for increased penicillin production. This increased production was prioritized and fully achieved by 1945 when industrial reactors saw 7 trillion units of penicillin manufactured.
The evolution of bioreactors has been swift ever since. Improvements to the production process include large-volume reactors, multi-vessel systems, and sterilization processes such as autoclave and freeze-drying.
Bacteria, until the 1990s, remained the principal aim of bioreactors; however, thanks to all the innovations and amendments to the process, the growth of cells belonging to other kingdoms, such as animal cells (including mammal and insect cells) and algae, resulted as a byproduct. A broader range of products, for example, vaccines, resulted from the versatility of using different types of cells.
Thus, despite the perception of bioreactors as a relatively new exploration into the world of science and fermentation, fundamental principles underpinning such technologies have been a part of human life for a long time. This long and rich history of the relationship between microorganisms, humans, cells, and reactors has yielded essential advances.
Moreover, all of the lessons learned throughout mean that we now have different designs for fermentors and various products and technologies that can help us build a healthier, more sustainable, and safer world.
The bioreactors manufactured at H.E.L (BioXplorer) are a prime example of this and have been used for removing greenhouse gases, such as CO2, or to produce biofuels in a greener way.
References and Further Reading
- https://www.pnas.org/doi/10.1073/pnas.0407921102
- https://www.acs.org/education/whatischemistry/landmarks/flemingpenicillin.html
- https://www.researchgate.net/publication/287302702_Application_of_different_types_of_bioreactors_in_bioprocesses
About H.E.L Group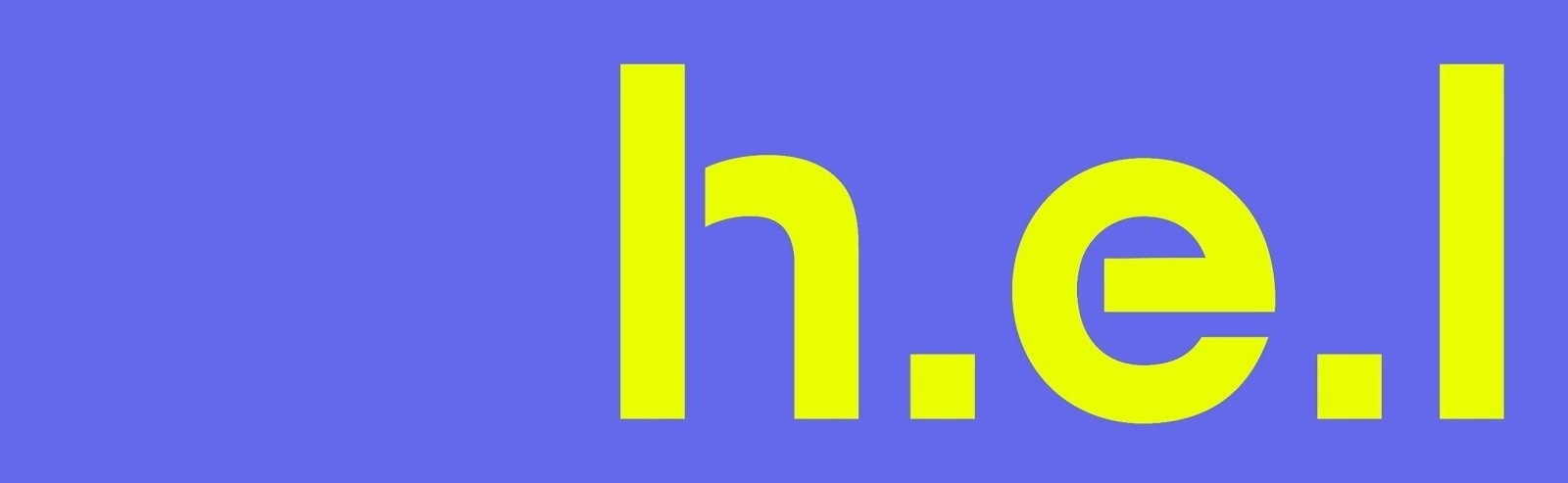
H.E.L develops and manufactures innovative scientific instruments and software designed to optimize the efficiency, safety, and productivity of key processes in chemistry and biology applications.
The H.E.L team of 70 includes highly skilled process and software engineers, based at their extensive research and manufacturing facilities in the UK, as well as sales and support offices around the world.
H.E.L has a long history of solving complex challenges for customers. Since 1987, the Company has worked with businesses and laboratories globally, providing proprietary automated solutions for the pharma, biotechnology, chemical, battery, and petrochemical sectors.
We continue to extend the reach of our products and service to support and enable R&D and process optimization further across Europe, the US, China, and India.
H.E.L is accredited with ISO 9001 : 2015
Sponsored Content Policy: AZoLifeScience.net publishes articles and related content that may be derived from sources where we have existing commercial relationships, provided such content adds value to the core editorial ethos of News-Medical.Net which is to educate and inform site visitors interested in medical research, science, medical devices and treatments.